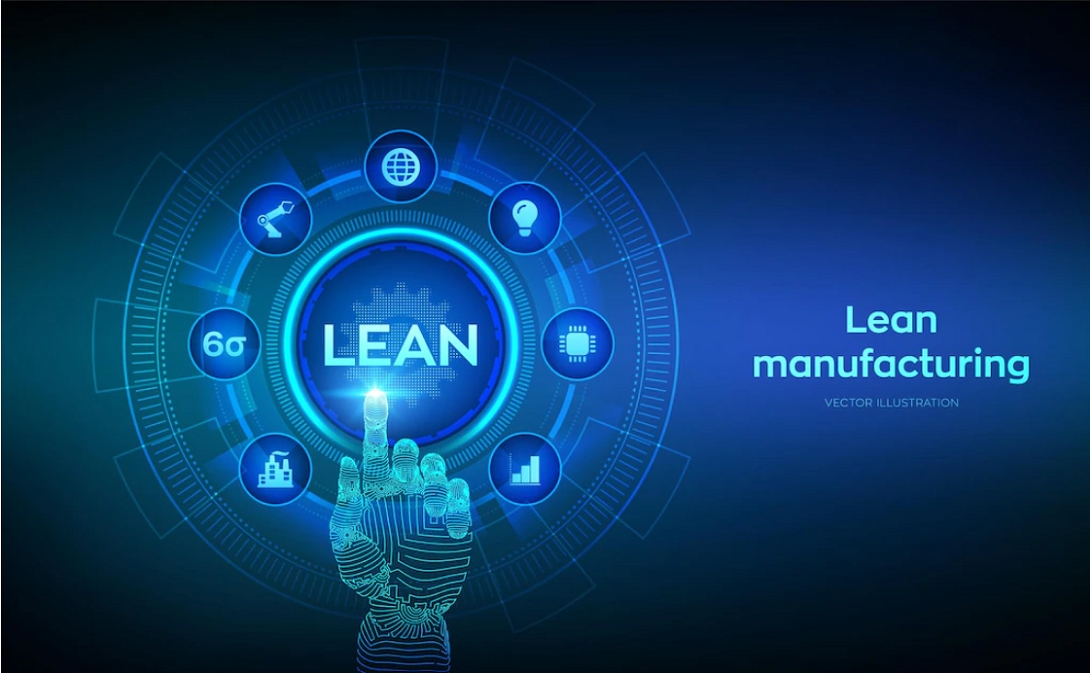
Để thực hiện được điều này, một giải pháp mang tên “Lean Manufacturing” (tạm dịch là “sản xuất tinh gọn”) hay còn được gọi tắt là “Lean” đã ra đời.
LEAN – Đũa thần thanh tẩy
(Bài viết được thực hiện vào năm 2006.)
Là một công ty sản xuất, không có gì tuyệt vời hơn nếu bạn tạo được chi phí sản xuất thấp, rút ngắn thời gian sản xuất mà sản lượng vẫn tăng, đáp ứng được mọi nhu cầu khách hàng và hơn hết là mang về lợi nhuận. Để thực hiện được điều này, một giải pháp mang tên “Lean Manufacturing” (tạm dịch là “sản xuất tinh gọn”) hay còn được gọi tắt là “Lean” đã ra đời từ Toyota. Nếu doanh nghiệp tầm cỡ như Toyota đã làm cuộc cách mạng của họ bằng Lean thì không có lý do gì chúng ta lại nghi ngờ việc dùng “chiếc đũa thần này” để biến đổi doanh nghiệp của mình.
Trong cuộc hội thảo “Ứng dụng Lean trong quản lý doanh nghiệp để gia tăng lợi nhuận” do Công ty Quản lý Quỹ Mekong Capital tổ chức, ông Andrew Cheah, chuyên gia tư vấn Lean, cũng là diễn giả chính của hội thảo đã đề nghị hàng trăm doanh nghiệp hàng tiêu dùng Việt Nam tham gia hội thảo kể ít nhất 2 khó khăn lớn mà họ đang gặp phải. Sau đó, ông Cheah tập hợp lại, thống kê và viết lên một bảng lớn 5 khó khăn chung ảnh hưởng đến lợi nhuận mà đa số doanh nghiệp chia sẻ. Đó là giá sản phẩm không cạnh tranh nổi trên thị trường; thời gian giao hàng chưa được đảm bảo; năng suất lao động của nhân viên kém; hàng tồn kho còn cao; dây chuyền sản xuất gián đoạn do phải chờ nguyên vật liệu. Và ông Cheah kết luận: “Đó là lý do vì sao quý vị có mặt trong buổi hội thảo Lean này!”.
![]() |
5 nguyên lý trong phương pháp Lean. |
Mục tiêu Lean đã được ông giải đáp ngay trong câu hỏi của một doanh nghiệp. “Tại sao tôi phải cần đến Lean?”, một doanh nghiệp hỏi, và ông Cheah trả lời: “Để loại bỏ những hoạt động lãng phí trong sản xuất mà không tạo ra giá trị tăng thêm, nhằm làm giảm chi phí sản xuất, tăng tính cạnh tranh và mang về lợi nhuận lớn”. Chúng ta hãy xem Lean, cỗ máy “sản xuất tinh gọn” đã làm thay đổi doanh nghiệp như thế nào?
LÀM SẠCH LÃNG PHÍ
Nếu bạn là một doanh nghiệp sản xuất, chắc chắn, sản phẩm bạn làm ra phải được dựa trên những gì khách hàng yêu cầu và sẵn lòng trả tiền để có được. Để có một sản phẩm, các hoạt động sản xuất của doanh nghiệp được chia làm 3 nhóm:
Thứ nhất, các hoạt động tạo ra giá trị tăng thêm, là hoạt động chuyển vật tư trở thành đúng sản phẩm mà khách hàng yêu cầu. Thứ 2, các hoạt động không tạo ra giá trị tăng thêm, là hoạt động không cần thiết cho việc chuyển vật tư thành sản phẩm mà khách hàng yêu cầu và những gì làm tăng thêm thời gian, công sức hay chi phí không cần thiết đều được xem là không tạo ra giá trị tăng thêm. Thứ 3, các hoạt động cần thiết nhưng không tạo ra giá trị tăng thêm, là các hoạt động không tạo ra giá trị tăng thêm từ quan điểm của khách hàng nhưng lại cần thiết trong việc sản xuất ra sản phẩm, như mức tồn kho cao được yêu cầu dùng làm kho dự phòng có thể được giảm thiểu khi hoạt động sản xuất trở nên ổn định hơn.
Nếu chúng ta lấy 100% là tỉ lệ chuẩn cho 3 nhóm hoạt động sản xuất nêu trên thì Trung tâm Nghiên cứu Doanh nghiệp Lean tại Anh đã đưa ra một con số khảo sát có thể làm các doanh nghiệp giật mình. Đó là trong 100% ấy thì hoạt động tạo ra giá trị tăng thêm chỉ là 5%, trong khi hoạt động không tạo ra giá trị tăng thêm lên đến 60% và hoạt động cần thiết nhưng không tạo ra giá trị tăng thêm là 35%. Điều đó có nghĩa, chúng ta đang lãng phí đến hơn 60% hoạt động sản xuất không xuất phát từ yêu cầu của khách hàng. Đó là lý do khiến doanh nghiệp đối mặt với chi phí sản xuất tăng, kéo giá thành phẩm tăng dẫn đến sức cạnh tranh và lợi nhuận giảm. Lean chính là công cụ góp phần làm giảm 60% lãng phí ấy.
7 MŨI TÊN VÀNG CỦA LEAN
Mục tiêu ngắn gọn của Lean là làm sao với cùng một mức sản lượng đầu ra nhưng có lượng đầu vào thấp hơn (ít thời gian hơn, ít mặt bằng hơn, ít nhân công hơn, ít máy móc hơn, ít vật liệu hơn, ít chi phí hơn). Chính việc làm “ít” lại lượng đầu vào sẽ giúp doanh nghiệp tinh gọn hiệu quả hoạt động sản xuất. Nếu sử dụng thiết bị và mặt bằng hiệu quả sẽ dẫn đến chi phí khấu hao trên đơn vị sản phẩm thấp hơn, nếu sử dụng lao động hiệu quả sẽ dẫn đến chi phí nhân công cho mỗi đơn vị sản phẩm thấp hơn và nếu mức phế phẩm thấp hơn sẽ làm giảm giá vốn bán hàng.
![]() |
Mô hình các lợi ích từ phương pháp Lean. |
Do đó, Lean nhắm đến 7 mục tiêu vàng: 1) giảm phế phẩm, 2) giảm thời gian quy trình và chu kỳ sản xuất bằng cách giảm thời gian chờ đợi giữa các công đoạn, 3) giảm thiểu mức hàng tồn kho ở tất cả các công đoạn sản xuất, 4) cải thiện năng suất lao động bằng cách giảm thời gian nhàn rỗi của công nhân và tránh những công việc hay thao tác không cần thiết của họ, 5) sử dụng thiết bị và mặt bằng hiệu quả bằng cách loại bỏ trường hợp ùn tắc và giảm thiểu thời gian dừng máy, 6) sản xuất nhiều loại sản phẩm khác nhau với chi phí và thời gian chuyển đổi thấp nhất, 7) kết hợp mục tiêu 1 và 6 sẽ góp phần làm giảm giá thành sản xuất, tăng sản lượng.
Nếu Lean là công cụ cho quy trình sản xuất tinh gọn với 7 mục tiêu như vậy thì đâu là bằng chứng hiệu quả của giải pháp này? Ở Mỹ, trong một bài điều tra của Tạp chí Industry Week thống kê, các công ty đang triển khai Lean của quốc gia này đã giảm được trung bình 7% giá vốn sản phẩm và có hơn 36% doanh nghiệp sản xuất đã và đang trong quá trình triển khai Lean.
Lantech, một công ty sản xuất thiết bị của Mỹ, cũng hoàn tất việc triển khai Lean năm 1995 với kết quả khả quan hơn rất nhiều so với hệ thống sản xuất theo lô sản phẩm năm 1991 với mặt bằng sản xuất trên mỗi máy giảm 45%, phế phẩm giảm 90%, chu kỳ sản xuất giảm từ 16 tuần xuống còn 5 ngày 14 giờ và thời gian giao hàng giảm từ 4-20 tuần xuống còn 1-4 tuần. Công ty sản xuất trang phục dành cho ngư dân Simms Fishing Products sau khi áp dụng Lean cũng làm cho tổng thời gian quy trình sản xuất giảm từ 17 ngày xuống chỉ còn 2-3 ngày.
Ở châu Á, năm 2005, tổng lợi nhuận của Tập đoàn Toyota nhiều hơn cả General Motors cùng với Ford và Chrysler gộp lại. Và trong khi General Motors chuẩn bị sa thải gần 30.000 công nhân cũng như đóng cửa hàng chục cơ sở sản xuất thì Toyota mở rộng thêm nhà xưởng ở Mỹ và nhiều nơi trên thế giới. Đâu là bí quyết thành công của Toyota? Chính là Lean! Ở Việt Nam, Lean là thuật ngữ còn mới mẻ. Và vì không hiểu rõ cốt lõi của quy trình sản xuất tinh gọn mà doanh nghiệp có thể đã đi từ lãng phí này đến lãng phí khác.
NHỮNG LÃNG PHÍ ẨN
Thực tế, rất nhiều doanh nghiệp Việt Nam mà Nhịp Cầu Đầu Tư từng khảo sát mặc dù biết rõ chi phí sản xuất thấp là một lợi thế để sản phẩm cạnh tranh được trên thị trường (giống như mục tiêu Lean nhắm tới) nhưng lại hiểu sai lệch rằng, để làm được điều này, họ phải cắt giảm chi phí như cắt lương nhân viên, mua vật liệu rẻ tiền… Trong khi đó, cốt lõi của Lean là giảm lãng phí (xem Box: Những loại lãng phí chính cần giảm).
Ông Cheah khẳng định, Lean là để giảm lãng phí chứ không phải giảm chi phí. Việc giảm chi phí không những không giảm được chi phí mà còn hình thành lãng phí ẩn, rủi ro ẩn mà doanh nghiệp sẽ đối mặt trong tương lai. Ví dụ, nếu cắt lương nhân viên, tinh thần làm việc của họ sẽ sa sút, dẫn đến năng suất lao động kém. Nhập nguyên vật liệu rẻ tiền sẽ sản sinh những thành phẩm kém chất lượng, dẫn đến mất khách hàng. Đó là lý do các chuyên gia Lean đánh giá, mức độ lãng phí trong hoạt động sản xuất của doanh nghiệp Việt cao hơn nhiều so với doanh nghiệp Mỹ.
![]() |
Ông Andrew Cheah, chuyên gia tư vấn Lean khẳng định, Lean là để giảm lãng phí chứ không phải giảm chi phí. |
Lean hoàn toàn có thể áp dụng cho các doanh nghiệp Việt Nam, không chỉ ở lĩnh vực sản xuất mà còn trong cả lĩnh vực dịch vụ.
Về sản xuất, một công ty may Việt Nam có quy mô 800 công nhân đã ứng dụng thành công bước đầu công cụ Lean. Trước đó, công ty này hay gặp khó khăn trong việc giao hàng đúng hẹn. Những chậm trễ này do ảnh hưởng từ quy trình sản xuất. Để đảm bảo uy tín với đối tác, công ty có lúc buộc phải chuyển hàng bằng đường hàng không. Điều này lại càng làm tăng cao chi phí vận chuyển. Sau khi ứng dụng Lean, hoạt động sản xuất được tinh gọn, sản phẩm của công ty càng đa dạng về chủng loại, giá thành và thời gian giao hàng luôn đáp ứng nhu cầu của khách, đặc biệt là họ đã giải phóng được 20% mặt bằng so với trước kia. Về dịch vụ, có thể đơn cử trường hợp Công ty Toyota Bến Thành. Là một trung tâm dịch vụ bảo trì xe của Toyota ở Việt Nam, Toyota Bến Thành qua quá trình áp dụng Lean đã giảm thiểu đáng kể quy trình dịch vụ bảo trì xe từ 240 phút xuống chỉ còn khoảng 50 phút/xe và tăng lượng xe được bảo trì trong ngày từ 4-6 xe lên 16 xe tại mỗi điểm bảo trì.
LEAN VÀ THUYẾT KAIZEN
Theo đánh giá của các chuyên gia, một số thay đổi do Lean đặt ra có thể gây gián đoạn hoạt động sản xuất nếu không áp dụng đúng, đồng thời một vài phương diện của Lean không thể áp dụng cho mọi công ty.
Vì thế, trước hết, chủ doanh nghiệp nên mời một chuyên gia Lean để tư vấn việc triển khai Lean. Giá thuê một chuyên gia Lean nước ngoài khoảng 2.000-2.500 USD/ngày. Chuyên gia này thông thường làm việc với doanh nghiệp trong 1 tuần để giới thiệu các ứng dụng, công cụ Lean, tìm phương pháp ứng dụng Lean tốt nhất cho doanh nghiệp.
Thứ 2, cũng như bất kỳ dự án quan trọng nào khác về cải tiến quy trình, sự cam kết và hỗ trợ của cấp lãnh đạo cao nhất là điều cần thiết.
Thứ 3, theo lời khuyên của các chuyên gia Lean, doanh nghiệp Việt Nam bước đầu chỉ nên triển khai Lean từng phần với các bước đơn giản như: 1) đo lường, theo dõi công suất và sản lượng của thiết bị, 2) thiết lập và tài liệu hóa các quy trình sản xuất rõ ràng hơn, 3) triển khai hệ thống 5S (xem Box) trong quản lý nhà xưởng và 4) quy hoạch lại cách bố trí mặt bằng sản xuất.
Thứ 4, như đã nói, vì việc ứng dụng Lean có thể làm gián đoạn sản xuất, nhất là khi doanh nghiệp chuyển đổi từ hệ thống “đẩy” sang “kéo”. Khái niệm trọng tâm của Lean là “Pull Production” (sản xuất kéo), trong đó luồng sản xuất trong nhà máy được điều tiết bởi yêu cầu từ công đoạn cuối quy trình “lôi kéo” hoạt động của các công đoạn đầu quy trình, vốn trái ngược với hoạt động sản xuất truyền thống theo lô sản phẩm mà trong đó hoạt động sản xuất được thúc đẩy từ đầu quy trình đến cuối quy trình dựa trên lịch sản xuất định kỳ. Vì thế, các chuyên gia khuyên rằng, chỉ nên thử nghiệm ở một bộ phận nhỏ (trên một dây chuyền sản xuất hoặc một chuỗi quy trình nhỏ) trong hoạt động trước khi áp dụng cho toàn bộ hoạt động sản xuất, đồng thời thuyết phục nhân viên trong công ty về lợi ích của Lean.
![]() |
Trong Lean còn có công cụ “Kaizen”, tiếng Nhật có nghĩa là “cải tiến liên tục”. |
Song, thực hiện Lean không có nghĩa “chỉ làm một lần rồi thôi”. Trong Lean còn có công cụ “Kaizen”, tiếng Nhật có nghĩa là “cải tiến liên tục”. Kaizen đã chứng minh, những doanh nghiệp thực hiện Lean thường xuyên, nghĩa là liên tục xác định các nguyên nhân tiềm tàng trong những hoạt động không tạo ra giá trị tăng thêm và loại bỏ chúng bằng cách cải tiến quy trình sản xuất, thì thường thành công trong việc ứng dụng Lean hơn các doanh nghiệp chỉ làm một hay vài lần.
HỆ THỐNG 5S 5S bao gồm các hướng dẫn tổ chức, sắp xếp khu vực làm việc của công nhân nhằm tối ưu hiệu quả công việc. • Sàng lọc (Sort): Phân loại những gì cần thiết và không cần thiết, để những thứ thường dùng đến luôn có sẵn và dễ tìm thấy. • Sắp xếp (Set In Order): Sắp xếp những thứ cần thiết theo thứ tự dễ lấy. • Sạch sẽ (Scrub): Giữ máy móc và khu vực làm việc sạch sẽ. Một số công ty cho sơn nơi làm việc và thiết bị với màu sáng nhằm tăng độ chiếu sáng. • Sẵn sàng (Standardize): Quy định rõ các thủ tục thực hiện những công việc sàng lọc; sắp xếp và giữ sạch sẽ. • Sâu sát (Sustain): Khuyến khích, truyền đạt và huấn luyện về 5S để biến việc áp dụng trở thành một phần của văn hóa công ty. (Nguồn: Mekong Capital) |
NHỮNG LOẠI LÃNG PHÍ CHÍNH CẦN GIẢM • Sản xuất dư thừa (Over-Production): Là sản xuất nhiều hơn hay quá sớm hơn yêu cầu một cách không cần thiết. Điều này làm gia tăng rủi ro bị lỗi thời, rủi ro về sản xuất sai chủng loại sản phẩm và có nhiều khả năng phải bỏ đi dưới dạng phế liệu. • Khuyết điểm (Defects): Bên cạnh các khuyết điểm về mặt vật lý trực tiếp làm tăng chi phí hàng hóa, khuyết điểm cũng bao gồm các sai sót về giấy tờ, cung cấp thông tin sai lệch về sản phẩm, giao hàng trễ, sử dụng quá nhiều nguyên vật liệu… • Tồn kho (Inventory): Lãng phí về tồn kho nghĩa là dự trữ quá mức cần thiết về nguyên vật liệu, bán thành phẩm và thành phẩm. Lượng tồn kho phụ trội dẫn đến chi phí tài chính cao hơn về tồn kho, chi phí bảo quản cao hơn và tỉ lệ khuyết điểm cao hơn. • Di chuyển (Transportation): Di chuyển ở đây chỉ bất kỳ sự chuyển động nguyên vật liệu nào không tạo ra giá trị tăng thêm cho sản phẩm. Ví dụ, việc di chuyển giữa các công đoạn xử lý làm kéo dài thời gian chu kỳ sản xuất, dẫn đến việc sử dụng lao động và mặt bằng kém hiệu quả, có thể gây nên những đình trệ trong sản xuất. • Chờ đợi (waiting): Chờ đợi là thời gian công nhân hay máy móc nhàn rỗi bởi sự tắc nghẽn hay luồng sản xuất trong xưởng thiếu hiệu quả. Điều này làm tăng thêm chi phí đáng kể do chi phí nhân công và khấu hao trên từng đơn vị sản lượng bị tăng lên. • Thao tác (Motion): Các chuyển động tay chân hay việc đi lại không cần thiết của công nhân không gắn liền với việc gia công sản phẩm. Ví dụ, việc đi lại khắp xưởng để tìm dụng cụ làm việc hay thậm chí các chuyển động cơ thể không cần thiết làm chậm tốc độ làm việc của công nhân. • Sửa sai (Correction): Sửa sai hay gia công lại bởi vì nó không được làm đúng trong lần đầu tiên, làm gián đoạn luồng sản xuất thông thoáng, dẫn đến những ách tắc và đình trệ trong quy trình. • Gia công thừa (Over-Processing): Gia công thừa chất lượng hay công năng của sản phẩm mà khách hàng không yêu cầu. Ví dụ, đánh bóng hay làm láng thật kỹ những điểm trên sản phẩm mà khách hàng không quan tâm. • Kiến thức rời rạc (Knowledge Disconnection): Đây là trường hợp khi thông tin và kiến thức không có sẵn tại nơi hay vào lúc được cần đến. Ví dụ, thiếu thông tin về công thức phối trộn nguyên liệu, pha màu có thể làm đình trệ toàn bộ quy trình sản xuất hoặc tạo ra các sản phẩm lỗi do các lần “thử - sai” tốn rất nhiều thời gian. |